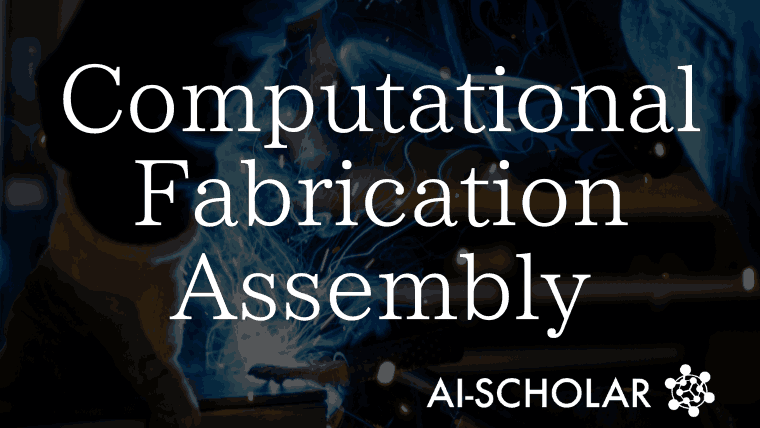
Manufacturing Revolution In The Shop Floor: Programmable Materials And Modular Assemblies At The Forefront
3 main points
✔️ Proposes a new platform to integrate multiple manufacturing processes to automate manufacturing and assembly
✔️ Using digital manufacturing technology and robotics to automate manufacturing and assembly at the machine, part, and material levels
✔️ Multi-process manufacturing machines, modular self-assembly, and program Validation on three themes of possible materials
Computational Fabrication and Assembly for In Situ Manufacturing
written by Martin Nisser
[Submitted on 21 May 2024]
Comments: MIT PhD Thesis 2024
Subjects: Robotics (cs.RO); Emerging Technologies (cs.ET)
code:
The images used in this article are from the paper, the introductory slides, or were created based on them.
Summary
Manufacturing now relies on large machines distributed across a wide range of industrial facilities, which are operated by specialists to build and assemble artifacts from many parts in stages. This traditional centralized mass production paradigm is characterized by large capital costs and inflexibility to changing needs, complex global supply chains dependent on economic and political stability, and uniform artifacts that cannot meet the technical and personal needs of today's diverse individuals and use cases characterized by overproduction and disposal.
These challenges are especially acute in the space environment. The space environment is remote and unpredictable, and the ability to manufacture in situ provides unique opportunities to address new challenges. However, the challenges faced in space are also common on Earth. In hospitals, disaster sites, low-resource environments, and laboratories, the ability to manufacture artifacts on the fly to meet needs can greatly enhance the ability to respond quickly to unexpected events.
This paper presents a digital manufacturing platform that leverages robotics and human-computer interaction tools to automate the manufacture of customized artifacts on the fly. Emphasizing three research themes of manufacturing machines, modular assembly, and programmable materials, the paper discusses the manufacturing of functioning robots, modular robotic platforms for space assembly in microgravity, and magnetic material programming methods for selective assembly.
Introduction
Manufacturing used to be the handcrafting of products to meet individual needs. As industrialization progressed, however, first textiles and then a variety of other products were mass-produced at low cost, and as the economy expanded, so did the standard of living for many people. More than 100 years have passed since the first Model T was built at Ford's Detroit plant, and with the exception of organizational innovations such as the Lean manufacturing system advocated by Toyota in the 1950s, manufacturing in the early 21st century used essentially the same methods as 100 years ago.
In recent decades, however, the proliferation of digital manufacturing technologies has revived the ability to manufacture products according to individual needs. Moore's Law has dramatically reduced the price and size of manufacturing machinery, and the proliferation of computer-aided design (CAD) tools and the evolution of generative models have fundamentally transformed manufacturing by allowing non-experts to design products.
Traditional manufacturing profited from the mass production of large numbers of uniform parts using super-specialized machinery that required enormous capital costs. However, the cumulative costs of this mass production and mass consumption have become apparent, as has the burden on the environment. The World Economic Forum reports that by 2022, manufacturing will account for one-fifth of global carbon emissions and more than half of global energy consumption.
Advances in digital manufacturing technology and robotics have set manufacturing on a new path. Featuring digital design, automation, and customization, and at a lower cost than traditional manufacturing infrastructure, digital manufacturing platforms such as 3D printing, CNC machining, and laser sintering are gaining popularity In 2015, the production of end-product parts accounted for 51% of additive manufacturing services In 2015, the production of end-product parts accounted for 51% of all additive manufacturing services. Leading manufacturers have embraced additive manufacturing technology to mass produce flagship products, and in 2014 a ratchet was 3D printed on the International Space Station. And the fuel injector for the European Space Agency's Ariane 6 rocket, once composed of 248 individually machined parts, is now 3D printed as a one-piece molded nickel alloy.
Thus, the development of digital manufacturing technologies has enabled on-site manufacturing of personalized hardware, creating new opportunities for rapid and customized production of products to meet specific needs. The implementation of such technologies is especially important in space environments, hospitals, disaster sites, and laboratories. The traditional centralized mass production paradigm makes it difficult to tailor products to individual needs and applications, as it relies on supply chain constraints and economic and political stability.
This paper presents methods for automating manufacturing and assembly at three levels
- Machine Level: Manufacturing machines that integrate multiple manufacturing processes.
- Component Level: Modular assemblies that allow reconfiguration of components.
- Material Level: Programmable materials where the material itself is programmed and assembled.
This will allow for on-site manufacturing and assembly automation, enabling the production of advanced functional artifacts at a variety of scales and applications, including robotics, space structures, and molecular machines. In addition, software tools for these hardware platforms will be presented to enable users to define design and assembly protocols.
As shown in Figure 1.1, this paper presents a method for automating manufacturing and assembly using these hierarchical assembly techniques.
Figure 1.1: Machine level, component level, and material level. In this paper In this paper, (1) multi-process manufacturing machine, (2) modular assembly platform, (3) material level (2) modular assembly platform, (3) programmable material. |
Related Research
The following is a brief summary of the major research areas relevant to this paper.
1. manufacture of circuit traces for electromechanical devices:.
- Methods to improve existing manufacturing machinery and automatically incorporate electronic components are being studied.
- An example is the technique of adding a coil-winding mechanism to a 3D printer to supply conductive wire at the same time as the filament.
2. expansion of existing manufacturing machinery: 1.
- Techniques have been developed to selectively ablate conductive films and place electronic components using a laser cutter.
- Techniques are being investigated that use laser sintering to sinter silver traces to create highly conductive circuit traces.
3. modular self-assembly reconfiguration:.
- Self-reconfigurable robots using cube modules have been developed, which allow reconfiguration in two and three dimensions.
- This includes a technique that uses electromagnets to achieve actuation between modules.
4. modular self assembly with folding
- Techniques for folding low-profile sheets into a three-dimensional structure using shape memory polymers and shape memory alloys are being investigated.
- This includes techniques that use lasers or localized heating to activate actuators.
5. stochastic self-assembly:.
- Methods for stochastic self-assembly using inexpensive cubic modules have been studied.
- Use magnetic pixels to create modules that are programmed to combine only in specific configurations.
6. programmable magnetic materials:.
- Using Hadamard matrices, techniques have been studied to program an array of magnetic pixels to self-assemble into a specific shape.
- This demonstrates a program that is generalizable to materials of different scales.
As shown in Figures 3.1 through 3.7, these technologies have many potential applications, especially the latest research in laser-based sintering and dynamic motion-signaling techniques. In particular, Figure 3.1 shows a hardware add-on that extends the laser cutter to create circuit traces and place electronic components.
Multi-process manufacturing machinery
This section details manufacturing machines that integrate multiple manufacturing processes. It includes the following
Hardware add-ons
A hardware add-on has been developed to extend the existing laser cutter. The add-on includes a silver dispenser and a pick-and-place mechanism for placing components, which allows the creation of circuit traces and the placement of electronic components (Figure 3.1).
Figure 3.1: LaserFactory is an integrated manufacturing process that creates fully functional devices. It is an integrated manufacturing process that creates devices. (a) The hardware added to the existing laser cutter consists of a silver dispenser and a pick-and-place mechanism. and a pick-and-place mechanism to not only cut shapes, but also create circuit traces and assemble electronic components. Create circuit traces and assemble electronic components. Our accelerometer-based motion add-on allows interfacing with the laser cutter without firmware changes. |
Hardware Mounting
As shown in Figure 3.3, the hardware add-on is attached to the laser head and consists of a mechanism that creates a silver trace and positions electronic components. An accelerometer is also used to detect motion signaling and control the add-on's movement.
Figure 3.3: Hardware add-ons. Physical device. This add-on consists of a silver dispenser for creating circuit traces and a pick-and-place mechanism for assembling electronic components. It consists of a pick-and-place mechanism for assembling electronic components. Attached to the laser head, the laser head is used to create the device geometry and cure the circuit traces. The image also shows an accelerometer for detecting motion that signals when the add-on should start/stop operation. The image also shows the accelerometer used to signal the start/stop of the motion. |
Laser Sintering
A laser sintering technique using the attenuated power of a CO2 laser has been developed for sintering silver traces. This allows the creation of highly conductive circuit traces (Figure 3.2).
Figure 3.2: LaserFactory device creation: (a) cutting device geometry, (b) dispensing silver to form circuit traces, and (c) picking and placing components. (a) cutting device geometry, (b) dispensing silver to form circuit traces, (c) picking and placing components. Quadcopter rotor. (e) As the last trace cures, here the quadcopter lifts directly off the platform. |
Manufacturing Settings for Laser Sintering
The manufacturing settings for laser sintering are summarized in Table 3.1, which shows the process sequence, line operation, laser cutter settings, and silver dispenser and pick-and-place mechanism settings.
Table 3.1: Process settings. Columns from left to right show (a) process order, (b) line operation, (c) laser cutter settings, and (d) additional settings for silver dispenser and pick-and-place mechanism. Pick-and-place mechanism. The tilde indicates changing values. |
Creating Non-Plane Geometry
Laser sintering techniques can also be used to create 2.5D geometry by folding or to create discretized 3D geometry by cutting and pick-and-place the material substrate itself (Figure 3.4).
Figure 3.4: LaserFactory can be used to create (a) 2.5D shapes by folding and (b) discretized 3D shapes by cutting and pick-and-place of the material substrate itself. (b) Discretized 3D shapes by cutting and pick-and-place of the material substrate itself. |
Extended Dynamic Signaling for Laser Cutters
Using motion signaling technology, we have developed a way to extend existing manufacturing platforms without interfacing to software. This allows for signal calibration and real-time classification (Figures 3.6 and 3.7).
Filtered Accelerometer Data
As shown in Figure 3.6, the acceleration changes rapidly during the execution of the embedded pattern, and this characteristic is used to generate a control signal that starts/stops the signal.
Figure 3.6: Filtered accelerometer data during embedded pattern execution. During Pattern Execution When the pattern is executed, the (blue) acceleration produces a series of spikes of opposite sign. Continuous. (a,d) This characteristic template causes the (orange) error signal to fall below the (green) threshold. When below the (green) threshold, the control signal reverses to start/stop command, start/stop silver extrusion. (b) Period of constant speed is indicated by acceleration near 0. (c) Volatile operations, such as moving between consecutive traces, cause large errors. (c) Volatile operations such as moving between successive traces cause large errors and can be distinguished from the actual motion signal indications embedded in the production file. They can be distinguished from the |
Threshold Calibration for Signal Classification
Figure 3.7 illustrates the threshold calibration method for signal classification, using a data set to distinguish between positive signals and noise.
Figure 3.7: Threshold characteristics of the signal classifier. Signals are sampled and signals are sampled and signals are sampled to construct a true positive data set. to construct a true positive data set. are sampled to construct a dataset of true positives. These are modeled as a normal distribution, and thresholds are set at their intersections. Distinguish between signal and noise. |
Laser Factory Design and Applications
The Laser Factory design tool allows users to select parts from a parts library, draw geometry and circuit traces, and design devices (Figures 3.8 and 3.9). The design file is converted to machine instructions and the manufacturing process is executed.
Figure 3.8: LaserFactory pipeline: (a) Design tools: the user places components and draws geometry and circuit traces. (b) Visualization tools: The user can preview the design in 3D and visualize the manufacturing steps to debug the design. (c) Post-processing: Upon export, the design file is converted into machine instructions for the extended laser cutter. (d) Fabrication: i.e., cut the geometry, dispense silver for circuit traces, pick and place components, cure the silver to make the traces conductive, and sinter the components. Once fabricated, the device is fully functional. |
Figure 3.9: The user uses the design toolbar to design a device such as a quadcopter. (a,e) Place components from the parts library, (b,f) Route circuit traces, (c,g) Draw geometry lines, and (d,h) Use the export tool. Render the output of the visualization tool. |
Application Examples
Examples of applications for devices created using Laser Factory include self-deploying quadcopters, personalized wearable devices, and printed circuit boards (Figure 3.11).
Figure 3.11: Functional devices made with LaserFactory: (a) Liftable quadcopter. (b) Wristband with sensors capable of gesture recognition; (c) Printed circuit boards, especially H-bridges. |
Modular Self Assembly
This section details modular self-assembly through reconfiguration.
Actuator
This study proposes a method of achieving actuation between modules using electromagnets built into each cube edge. This allows the modules to pivot using repulsive forces between same poles and attractive forces between different poles (Figures 4.1 and 4.2).
Figure 4.1: Four Electrovoxels are electromagnetically actuated modules that can be reconfigured in three dimensions under microgravity using embedded electromagnets. They can be reconstructed in three dimensions under microgravity using embedded electromagnets. |
Figure 4.2: Reconfiguration operations for (top) turning and (bottom) rolling. Electromagnets are shaded red and blue to show their polarization relative to the global coordinate system. Same polarity repels and opposite polarity attracts. |
Electromagnet Parameters
Electromagnet parameters include details such as the number of electromagnets, number of windings, and current value, which control the actuation force (Figure 4.4).
Figure 4.4: Calculation of the electromagnet force. Here D1,D2=10 and one turn coil to coil (force vector in magenta). |
Dynamic Models
The dynamic model uses a mass point model to simulate force vectors and module motion. This model allows us to analyze the dynamic interaction between modules (Figure 4.5).
Figure 4.5: Dynamical model. A massless link of length L (solid line) connects a point mass m. The force F actuates the pivot by repulsion, and G attracts the electromagnet to form a new stable coupling. |
Hardware (Esp. Computer)
The hardware design includes both electronics and mechanical design. The placement of electromagnets and electronic components, as well as the mechanical structure of the module, are detailed (Figures 4.6 and 4.7).
Figure 4.6: Printed circuit board design. (left) Schematic, page 1 of 2 (right) Layout, board 1/2. |
Figure 4.7: Module design iterations. (left) first prototype to (right) final prototype. |
Figure 4.8: CAD model of the cube module. |
Electronic Circuit Board Design
The circuit board design diagram shows the placement and connections of electronic components within the module (Figure 4.6).
Experiments and Results
2D and 3D self-reconstruction experiments were performed on an air table and in a microgravity environment during parabolic flight (Figure 4.12).
Figure 4.12: Two elements performing a turning maneuver (a). (a) On an air table used to simulate a microgravity environment in a 2D maneuver. (b) 3D maneuver in microgravity. |
Simulation Results
Simulation results show the planning of pivoting and moving operations, which assesses the success rate of reconfiguration (Figures 4.3 and 4.9).
Figure 4.3: Web simulation for planning the reconfiguration and calculating the associated electromagnetic commands. (A) Pre-scripted operations. (B) Viewport. (C) Configuration. |
Figure 4.9: Reconfiguration between chair, table, and sofa |
Experiment Results
The 2D and 3D experimental results include measurements of the success rate of the reconfiguration and the force between the modules. In particular, Figure 4.11 shows the force versus current and electromagnet separation distance.
Figure 4.11: Force v current and electromagnet separation distance showing raw data for N=5 and average ±1 St.D. For comparison, the relationship between force and distance predicted from (4.2) is shown. |
Discussion
Based on experimental results, the scalability and practicality of reconfigured robots will be discussed. In particular, issues such as cost, complexity, and size requirements will be examined and suggestions will be made for the design of scalable self-reconfiguring robots.
Modular Self Assembly with Folding
Modular self-assembly with folding is detailed.
Algorithm
An algorithm has been developed to generate collapsible 3D geometry. The algorithm shows how to create a 3D structure by developing a 3D mesh into a planar sheet and then pulling the sheet (Figure 5.1).
Figure 5.1: Our digital fabrication pipeline allows users to rapidly prototype 3D objects. a) A web-based tool for uploading and rendering 3D meshes. This tool performs (B) an unpacking algorithm that expands the mesh into a flat sheet divided into planar sheets with through-holes. (C) This unfolded shape is then machined with a laser cutter, threaded through the holes, and the sheet is folded into the desired structure by pulling the threads. |
Vertex Set Identification
As shown in Figure 5.2, we identify the vertex sets and calculate the direction of threading to join them. The depth of the vertex set is taken into account and only the necessary joints are made, thus minimizing the amount of thread required.
Figure 5.2: (A) Illustration of the algorithm that identifies the set of vertices that need to be joined by a string. The colors represent the vertices of the net to be joined, and the numbers represent the depth of rigidity of each vertex. The small arrows indicate the search direction from each vertex. Furthermore, vertices with a stiffness depth of 1 do not need to be joined by a string to assemble the final cube; in the 3D inset, the cut edges are indicated by dotted lines. (B) The same concept is shown with a piece of dodecahedral net. The vertices at depths 1 and 2 do not necessarily need to be joined in order to determine a fully joined geometric structure. Adding strings between all these vertex pairs would require at least twice as much string and would likely complicate the assembly process by requiring several sharp turns in its path, which would increase friction during assembly. Depending on the function of the assembled object and the expected loads, this may be a worthwhile trade-off to increase the rigidity of the final structure. |
Web Tool
A web-based tool was developed to allow users to upload a 3D mesh, apply the folding algorithm, and view the computed expanded net (Figure 5.3).
Figure 5.3: Web-based visualization tool. (A) This interface allows the user to upload a geometry file or select a geometry file, apply the folding algorithm to that geometry, and render the computed perforated net. The perforated net is displayed at each stage of the folding procedure. (B) The steps of the folding process can be visualized. |
Manufactured Structure and Application
Structures manufactured using this method come in a variety of shapes and scales and serve a range of applications, from educational tools to load-bearing furniture (Figures 5.4 and 5.5).
Figure 5.4: Structures manufactured using our pipeline range in scale from regular polyhedral to organic. to and at scales ranging from load-bearing to aesthetic; including VR, educational, and functional load-bearing contexts. |
Figure 5.5: Fabrication of polyhedra. (A) Unpacked layout of four simple 3D solids (B,C,D,E) Structures fabricated during folding. |
Manufacturing Polyhedra
Figure 5.5 shows an example of a polyhedra manufactured using a simple 3D solid unfolding layout. By pulling the sheet through the thread, it is folded into the target shape.
Manufacturing Organic Shapes
Figure 5.6 illustrates Stanford Bunny's rendering, deployment, and fabrication process, which can also manufacture complex organic shapes.
Figure 5.6: Fabrication of organic shapes. (A) rendering, (B) unpacking, and (C) fabrication. Stanford rabbit. |
Example of A Pull-up Net
As shown in Figure 5.7, a stable folding operation can be achieved by pulling while securing one side of the deployment net.
Figure 5.7: Example of folding a 3D polyhedron using a pull-up net: by convention, one surface of the folding net (gray) remains fixed during the folding procedure, helping to stabilize the structure while the user manipulates the fold. |
Application Examples
As shown in Figure 5.8, there are a variety of applications ranging from educational kits to low-resolution physical props for VR to bookshelves and stools to support loads.
Figure 5.8: (A-D) Educational toolkit to teach the relationship between area and volume; (E) On-demand production of low-resolution physical props for virtual reality; (F) Load-bearing applications such as bookshelves and stools. |
Discussion
The advantages and challenges of this approach are discussed. Particular emphasis is placed on its low cost and ease of fabrication, as well as its ability to use external power for powerful actuation. On the other hand, challenges in material selection and control of the folding operation are also discussed.
Programmable Materials
This section details programmable materials.
Encoding Generation
We have developed a method for generating programmable encodings of materials. This method uses magnetic pixels to create modules that are programmed to combine only in specific configurations (Figure 6.1).
Figure 6.1: (left) An inexpensive ($0.23) cubic module is used to enable stochastic self-assembly. (Top, right) This is accomplished by magnetically programming the faces of the module with uniquely mating pairs of Hadamard matrix-based encodings, and bounds on its performance are shown. (bottom, right) The key to the module's success is its ability to be strongly attracted to its oriented counterpart while being agnostic to all other translational, rotational, and non-oriented modules. |
Figure 6.2: Overview of the stochastic self-organization approach. (left) Magnetic Pixels: The cube module is programmed with a matrix of magnetic pixels. This allows the faces of the module to selectively mate and assemble the target shape. For clarity, we show a 3x3 matrix, but our modules use 8x8. (center left) Scalability: Our binary 8x8 matrix can encode 264 module faces with unique permutations, and the modules are inexpensive ($0.23). (center-right) Selectivity assurance: We use Hadamard matrices to encode magnetic pixels on a plane with two criteria. In the "local" case, mating planes are attracted to only one configuration; in the "global" case, nonmating planes are not attracted to any configuration. (Right) Reconfigurability: Encoding is "programmed" as magnetic pixels using magnets placed on the 3-axis CNC. The module can be reprogrammed to self-assemble to a new target geometry. |
Matrix Search
The matrix search algorithm is used to generate encoding patterns. It calculates the pixel placement of the normalized binary values according to the order of the Hadamard matrix (Figure 6.3).
Figure 6.3: (Top) Normalized natural-order Hadamard matrices generated by matrices of order N of 2, 4, 8, and 16. The binary values of -1 and -1 are represented as dark and light pixels, respectively. (Bottom) Its companion. |
Magnetic Plotter
As shown in Figure 6.6, a magnetic plotter mounted on a 3-axis CNC is used to program the magnetic pixels of the module. This allows for highly accurate programming.
Figure 6.6: Magnetic plotter: (a) Add-on mounted on a 3-axis CNC. (b) Electronics of the add-on viewed from above. (c) Close-up of the plotting end-effector, which consists of an electromagnet with a conical tip for writing and a Hall effect sensor for reading the magnetic program. |
Result
We evaluated the performance of programmable materials, including the reliability and maximum magnetic field strength of the magnetic program.
Maximum Value of Magnetic Field Strength
As shown in Figure 6.7, we evaluated the magnetic field strength at saturation of the electromagnet. This confirms the intensity of the programmed pixel.
Figure 6.7: B-H curve of an electromagnet. The electromagnet saturates at 0.34T at both (a) the positive ('North') and (b) the negative ('South') ends. |
Persistence of The Magnetic Field
Figure 6.8 shows the hysteresis curve of the sheet and evaluates the persistence of the magnetic field when the sheet is fully saturated and unsaturated.
Figure 6.8: Hysteresis curves of a sheet when it is fully saturated (major loop, blue) and when it is not fully saturated (minor loop, red). (a) positive and negative saturation, (c) positive and negative residual flux, (e) positive and negative coercivity. |
Accuracy of Magnetic Pixel Value Readings
Figure 6.9 shows a histogram of magnetic pixel values scanned using the Hall effect sensor, with north- and south-facing pixels clearly distinguished.
Figure 6.9: Histogram of magnetic pixel values scanned by the Hall effect sensor. North- and south-facing pixels are clearly distinguished. |
Predicted vs. Measured Interaction
Figure 6.10 evaluates the cross-correlation between the checkerboard pattern and the Hadamard matrix, comparing predicted interactions with actual measurements.
Figure 6.10: Predicted and measured magnetic interactions when two patterns of checkerboard and Hadamard matrices are cross-correlated with their negatives. |
Programmable DNA Assembly
We have developed an approach to apply the concept of programmable magnetic materials to DNA assembly. This allows for self-assembly at the nanoscale.
DNA Tile Design
We have developed a DNA tile design and manufacturing process as shown in Figure 6.18. This demonstrated that the programmed DNA tiles self-assemble into the desired shape.
Figure 6.18: Overview of the translation of a code-theoretic array for use in DNA assembly. (a) A four-valued alphabet of A, T, G, and C is used to translate a two-dimensional array instantiated as binary poles into a one-dimensional string. (c) We synthesize the actual DNA and instantiate the 1D code as a series of vacancies and overhangs designed to bind a particular overhang sequence to its complementary vacancy. (d) We designed the square tiles to hierarchically assemble into larger squares (left). Assembly by atomic force microscopy (right). |
Discussion and Future Research
In this section, we will summarize the study and discuss future research.
Research Summary
Based on advances in digital manufacturing and miniaturization of hardware, this thesis developed an integrated manufacturing technology to produce functional artifacts in the field on a single platform. This has created opportunities to manufacture highly functional artifacts at a variety of scales and applications, including robots, space structures, and molecular machines.
Multi-Process Manufacturing Machines
At the machine level, we have developed multi-process manufacturing machines, such as the Laser Factory, to automatically manufacture functioning quadcopters and health wearables (Figures 3.1 and 3.2).
Modular Self-Assembly
At the part level, modular self-assembly platforms such as Electrovoxel were used to achieve 2D and 3D self-reconfiguration (Figures 4.1 and 4.2).
Programmable Materials
At the materials level, magnetic materials and DNA have been used to develop programmable materials that self-assemble into specific shapes (Figures 6.1 and 6.2).
Future Research
Future research could focus on the following areas
-
Further integration of manufacturing machinery:.
- Develop technology to further integrate multiple manufacturing processes to produce artifacts with more advanced features.
- Improve the performance and flexibility of manufacturing machinery by integrating new materials and processes.
-
Extension of self-assembly technology:.
- Improve module design and actuation techniques to allow more complex shapes and structures to reconfigure themselves.
- Development of self-assembly technology for nanoscale and macroscale applications.
-
Programmable material applications:.
- Develop new encoding methods and materials to create programmable materials for a variety of environments and applications.
- Applied research for specific applications, such as medical or space exploration.
-
Development of user-friendly software tools:.
- Develop software tools that allow end users to easily define design and manufacturing protocols.
- Improve the user experience by improving the interface and adding automation features.
Conclusion
In this paper, we proposed a new platform that integrates multiple manufacturing processes with the goal of automating manufacturing and assembly at the shop floor. Specifically, the paper showed how advances in digital manufacturing technology and robotics can be leveraged to automate manufacturing and assembly at the machine, part, and material levels.
Major Contributions
-
Multi-process manufacturing machinery:.
- Development of hardware add-ons to create circuit traces and place electronic components.
- Silver trace sintering technology using CO2 laser.
- Extension of existing manufacturing platforms using dynamic signaling.
-
Modular Self-Assembly:.
- Proposal of a method to achieve module-to-module actuation using electromagnets.
- Development of a 3D self-reconfiguring robot using cube modules.
-
Programmable materials:.
- Development of modules that use magnetic materials and are programmed to couple only in specific configurations.
- Demonstration of self-assembly at the nanoscale using DNA.
These technologies have great potential for rapid on-site response and customized product manufacturing. In particular, they are expected to be applied in space environments, disaster sites, and other situations that are difficult to handle with conventional manufacturing methods.
Future Research
Future research will further develop the technology with the goal of further integrating manufacturing machinery, extending self-assembly techniques, and new applications for programmable materials. We also aim to enable end users to easily design products and define manufacturing protocols through the development of user-friendly software tools.
We hope that the technologies and methods proposed in this paper will be a step toward the future of manufacturing.
Categories related to this article