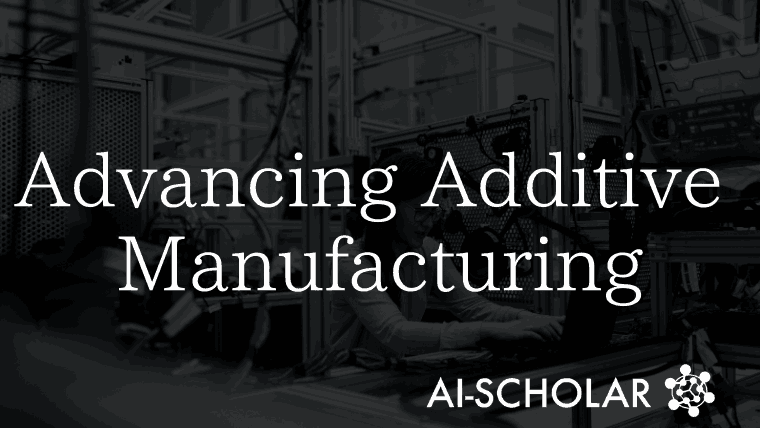
Advances In Additive Manufacturing Through Deep Learning
3 main points
✔️ An in-depth look at the innovative improvements that the application of DL (Deep Learning) in AM (Additive Manufacturing) processes can bring, as well as the current challenges and future opportunities associated with its application.
✔️ The convergence of AM and DL in the manufacturing industry has the Potential to revolutionize the production of customized products
✔️ However, there are still many challenges to be solved to make this a reality, such as generalizing DL models, managing data quality, and improving interpretability
Advancing Additive Manufacturing through Deep Learning: A Comprehensive Review of Current Progress and Future Challenges
written by Amirul Islam Saimon, Emmanuel Yangue, Xiaowei Yue, Zhenyu (James)Kong, Chenang Liu
[Submitted on 1 Mar 2024]
Comments: accepted by arXiv
Subjects: Machine Learning (cs.LG)
code:
The images used in this article are from the paper, the introductory slides, or were created based on them.
Summary
The intersection of Additive Manufacturing (AM) and Deep Learning (DL) has received increasing attention in recent years. This paper examines in detail the innovative improvements that the application of DL in AM processes can bring, as well as the current challenges and future opportunities associated with its application. In particular, it focuses on the following aspects:
-
- The complexity of the AM process and how DL can help us understand and control it
- Types of data needed to apply DL in AM and how to manage them
- Recent research on AM design, process modeling, process monitoring, and control using DL
The authors suggest that the fusion of AM and DL has the potential to revolutionize the production of customized products in manufacturing. However, there are still many issues to be resolved before this can be realized, such as generalizing DL models, controlling data quality, and improving interpretability. This paper aims to provide an overview of the current status and future directions of DL in the AM field and offer useful insights for researchers and practitioners.
Introduction
Value-added manufacturing (AM) is gaining importance as an innovative technology in the manufacturing industry, especially with the growing demand for customized products. AM is gaining attention in many industries because it reduces material waste and can produce parts with complex internal structures compared to conventional subtractive manufacturing methods. However, AM processes are by their nature complex and difficult to control, making consistency of quality a challenge.
Meanwhile, advances in deep learning (DL) technology are opening new possibilities for AM process optimization and quality control: DL can learn complex patterns from large amounts of data, enabling predictions, monitoring, and control of processes that were previously difficult. The authors point out that applying DL to AM offers the following advantages:
-
- Understanding the relationship between process parameters and final product quality
- Early detection and correction of defects in the manufacturing process
- Optimization of material use during the design phase
However, a number of challenges also exist, including the high dimensionality of AM data, noise issues, and the lack of interpretability of DL models. This paper examines in detail the current status of DL in AM and suggests future research directions. The authors conclude that the integration of AM and DL is the key to accelerating innovation in manufacturing.
AM Data Classification
Figure 1 shows AM data types and examples.
Figure 1: Overview of AM data |
- 1D data: acoustic emission (AE), temperature, pressure, humidity, etc.
- 2D data: 2D sections cut from 3D CAD geometry, 2D lattice structure images, powder bed images, molten pool thermal images, molten pool microstructure images, electron backscatter diffraction (EBSD) images, video data
- 3D data: point clouds, meshes, voxels (see Figure 2)
Figure 2: 3D representation of sample parts: (a) original, (b) voxel, (c) point cloud, (d) mesh
Intersection of DL and AM
Research Challenges and DL Potential
The application of deep learning (DL) in value-added manufacturing (AM) provides an effective means to address the complexity and dynamism of AM processes. The authors identify the following key challenges and examine how DL can address these challenges
- Process Complexity: AM is often a complex process involving multiple factors such as materials, thermal management, accuracy, etc. DL learns these complex interactions to help predict and optimize the process.
- High dimensionality of data: Data obtained from AM (e.g., 3D scan data, temperature distribution data) are often high-dimensional and difficult to handle with conventional analysis methods.
- Quality Control: DL can improve the quality of AM products by detecting and correcting defects that may occur in the manufacturing process at an early stage.
Figure 3 shows a schematic of the DL-compliant design for AM.
Figure 3: Schematic of deep learning-enabled design for AM
Importance of Data
The authors emphasize that the right quantity and quality of data is essential for effective training and evaluation of DL models. In particular, the types of data generated by the AM process include:
- Image data: obtained by photographing each layer during the manufacturing process or by 3D scanning the product.
- Sensor data: Data collected from sensors during the process, such as temperature, pressure, vibration, etc.
- Operational data: data on process parameters and manufacturing conditions, used for quality prediction and process optimization.
Literature Review and Methodology
The authors provide an extensive review of recent research on the application of DL in AM and how DL is used at various stages of AM. The review reveals that DL plays an important role in AM design, process optimization, and quality assurance. It also suggests directions for future research through analysis of best practices.
Design of AM by DL
Design Optimization
The use of deep learning (DL) in the AM process plays an important role in product design optimization. The authors provide examples of how DL contributes to the design phase by
- Design Automation: DL can automatically generate optimal product designs based on given performance requirements. This greatly improves the efficiency of the design process.
- Generate complex geometries: AM is well suited for manufacturing complex geometries, but DL opens up new design possibilities that have never been possible before.
Deviation from geometry
Predicting and compensating for geometric shape deviations that directly affect product quality is important in the AM process. The authors emphasize the effectiveness of DL in
- Prediction of shape dev iations: The DL model can predict in advance shape deviations that may occur during the manufacturing process. This allows design adjustments to be made prior to manufacturing to prevent defects before they occur.
- Proposed compensation strategy: DL can propose a strategy on how to compensate for anticipated deviations. This will help ensure the quality of the final product.
According to the authors, the use of DL is expected to revolutionize the design process in AM, improve product quality, and significantly increase manufacturing efficiency. design optimization and geometry deviation management with DL will be important research areas in the future of AM technology.
Table 4 lists papers that apply DL techniques for design optimization.
Table 4: Papers applying DL techniques for component design and design optimization
AM Process Modeling
Thermal profile modeling
One of the key determinants of quality and performance in the AM process is the thermal profile during manufacturing. The authors detail how this thermal profile can be accurately modeled and predicted using deep learning (DL) techniques. In particular, two approaches are highlighted
- Pure Data Driven DL (DDDL) models: These models predict thermal profiles based on large amounts of data taken from the AM process. For example, temperature profiles at different layers and temperature variation with time are modeled.
- DL (PIDL) model incorporating physical information: The PIDL model aims to predict thermal profiles more accurately by incorporating physical laws and process knowledge into the DL model. This allows for reliable modeling even when data is scarce.
Process and Structure Modeling
In the AM process, the final physical properties of the product are highly dependent on the fine process conditions during the manufacturing process. The authors propose a method for modeling these complex process structure property (PSP) relationships using DL. Specifically, the following applications are presented:
- Prediction of mechanical properties: The DL model can predict the mechanical properties of a product from AM process parameters. This enables material selection and optimization of process conditions during the design phase.
- Microstructure Analysis: The microstructure of a product has a significant impact on its performance, and DL can analyze these microstructures in detail from images and sensor data during the manufacturing process to aid in quality control.
The authors conclude that the use of DLs improves the quality and performance of products by providing a better understanding of the AM process. They also point out that modeling thermal profiles and PSP relationships with DL will play an important role in the development of AM technology.
Figure 4 shows a schematic of the modeling and Table 5 shows representative papers.
Figure 4: Schematic of data-driven AM
Table 5: Papers applying DL to AM thermal profile modeling.
Process Monitoring and Control
Monitoring and controlling the AM process is essential to assure product quality and consistency. The authors emphasize how deep learning (DL) plays an important role in this area and provide examples of how DL can contribute in the following ways
Image-based surveillance
Using real-time images of the manufacturing process, the DL model can detect defects and abnormalities. This allows for quicker response to problems and improved product quality.
DL can be applied to precise inspection of product surfaces to identify even the smallest defects. This helps to find defects that are often missed by conventional methods. Table 6 lists papers on monitoring. Figure 6 organizes the keywords.
Monitoring based on sensor signals
By analyzing sensor data (temperature, pressure, etc.) collected during the AM process, process conditions can be accurately monitored and controlled DL learns patterns from these data and immediately detects anomalies.
By integrating and analyzing data from multiple sensors, a more complete picture of the process can be obtained, which directly leads to improved product quality.
Point cloud based monitoring
Point cloud data from 3D scans can be analyzed by DL to detect deviations in dimensional accuracy and shape of products and improve the accuracy of the manufacturing process.
Process Control
Using the DL model, process parameters can be adjusted in real time to optimize product quality. This reduces scrap rates and improves production efficiency.
The impact of process parameters on specific product characteristics can be predicted by the DL model and the process can be automatically adjusted accordingly to guarantee the desired product characteristics. Figure 5 illustrates the main points of the monitoring and control paper. Figure 7 shows a flowchart for quantifying uncertainty in the AM process.
The authors conclude that process monitoring and control with DLs will lead to important advances in the future of AM, and as DLs evolve, more accurate and efficient AM processes are expected to become a reality.
Table 6: Figure 7 shows papers applying DL to monitoring based on porosity prediction.
Figure 5: High-level summary of the literature on process monitoring and control
Figure 6: Paper applying CNN-based models to image-based defect monitoring Quality assessment per AM process
Figure 7: Flowchart for uncertainty quantification in the AM process (Mahadevan et al. 2022)
Challenges and Future Directions
Integration of AM processes and deep learning (DL) has made great strides in the manufacturing industry, but several challenges exist in implementation. The authors propose future directions to address these challenges and encourage further development of AM and DL.
Improved ability to generalize models
To ensure that DL models are applicable to a wide variety of AM processes and complex product geometries, the generalization capability of the models must be improved. This can be achieved by learning from different data sources and utilizing transition learning techniques.
Data Quality and Accessibility
Ensuring high quality AM process data and access to these data is critical. Standardization of data collection protocols and development of open access databases will contribute to future research.
Ensure Interpretability and Reliability
Understanding the decision process and assessing the reliability of the DL model is a major challenge in applying DL to the AM process. Research is required to improve the interpretability of the model.
Uncertainty Management
It is important to develop a DL model that accounts for uncertainty in the AM process. Quantifying uncertainty and incorporating it into model predictions allows for more reliable decision making.
The authors point out that solutions to these challenges are key to accelerating the integration of AM and DL and to fostering innovation in manufacturing. It is hoped that researchers and practitioners will work in these directions to maximize the potential of AM and shape the future of manufacturing.
Conclusion
This paper provides an extensive review of the possibilities offered by the application of deep learning (DL) in value-added manufacturing (AM), the current challenges and future directions in its application, and shows that DL is a powerful tool that can contribute to AM process optimization, quality control, and product design innovation. The authors highlight the following points The authors emphasize the following points
-
- Design optimization and process modeling of AM by DL directly improves product quality and manufacturing efficiency.
- Applying DL to AM process monitoring and control can increase product consistency and reliability.
- Model generalization, data quality and accessibility, interpretability, and uncertainty management are important issues to be addressed in future research.
This paper demonstrates that the integration of AM and DL offers an important opportunity to promote innovation in manufacturing. Future integration of these technologies is expected to advance manufacturing processes and improve product quality. The authors conclude that the potential of AM can be further exploited by addressing the challenges raised by researchers and practitioners and by proceeding in the directions suggested.
Categories related to this article