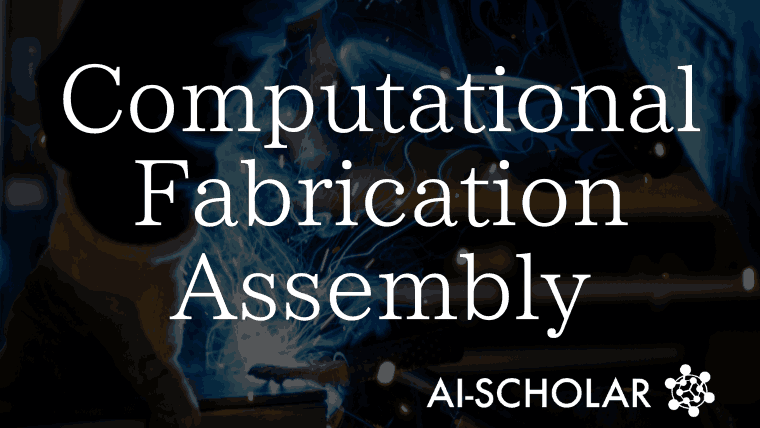
革新现场制造:可编程材料和模块化装配的前沿
三个要点
✔️ 提出一个整合多种制造工艺的新平台,以实现制造和装配自动化
✔️ 利用数字制造技术和机器人技术,在机器、组件和材料层面实现制造和装配自动化
✔️ 多工艺制造机器、模块化自组装和可编程材料对三种可能的材料主题进行验证
Computational Fabrication and Assembly for In Situ Manufacturing
written by Martin Nisser
[Submitted on 21 May 2024]
Comments: MIT PhD Thesis 2024
Subjects: Robotics (cs.RO); Emerging Technologies (cs.ET)
code:
本文所使用的图片要么来自论文、介绍性幻灯片,要么是参考这些图片制作的。
概述
现在的制造业依赖于分布在各种工业设施中的大型机器,这些机器由专家操作,分阶段制造和组装由许多部件组成的人工制品。这种传统的集中式大规模生产模式的特点是:资本成本高昂,无法灵活应对不断变化的需求;全球供应链复杂,依赖于经济和政治稳定;产品千篇一律,无法满足当今多样化的个人技术和个人需求以及使用情况。以过度生产和废弃为特征。
这些挑战在太空环境中尤为严峻。太空环境遥远而不可预测,原地制造的能力为应对新的挑战提供了独特的机会。然而,太空中面临的挑战在地球上也很常见。在医院、灾难现场、资源匮乏的环境和实验室中,原地制造人工制品以满足需要的能力可以大大提高快速应对突发事件的能力。
本文介绍了一个数字制造平台,该平台利用机器人技术和人机交互工具,可在飞行中自动制造定制工艺品。论文突出了三个研究主题--制造机器、模块化装配和可编程材料--讨论了功能机器人的制造、用于微重力空间装配的模块化机器人平台,以及用于选择性装配的磁性材料编程方法。
介绍
制造业曾经是为满足个人需求而手工制作产品。然而,随着工业化的发展,首先是纺织品,然后是一系列其他产品被廉价大规模生产出来,随着经济的发展,许多人的生活水平也随之提高。自福特底特律工厂制造出第一辆 T 型车以来,100 多年过去了,除了组织创新(如丰田在 20 世纪 50 年代倡导的精益生产系统)之外,21 世纪初的制造业使用的方法与 100 年前基本相同。
然而,近几十年来,数字化制造技术的普及重新唤起了根据个人需求制造产品的能力。摩尔定律大大降低了制造设备的价格和尺寸,计算机辅助设计(CAD)工具的广泛使用和生成模型的进步从根本上改变了制造业,使非专业人员也能设计产品。
传统制造业利用超级专业化的机器大量生产统一的部件,需要巨额的资本成本,从而从中获利。然而,这种大规模生产和消费的累积成本以及对环境的影响逐渐显现。世界经济论坛报告称,到 2022 年,制造业将占全球碳排放量的五分之一,占全球能源消耗的一半以上。
数字化制造技术和机器人技术的进步使制造业走上了一条新的道路。与传统制造基础设施相比,3D 打印、数控加工和激光烧结等数字化制造平台具有数字化设计、自动化和定制化等特点,且成本更低,因此已得到广泛应用。 2015 年,终端产品零件的生产占所有增材制造服务的 51的 51%。领先的制造商已采用增材制造技术批量生产旗舰产品,2014 年,国际空间站上的棘轮被 3D 打印出来。欧洲航天局阿丽亚娜6号火箭的燃料喷射器过去由248个单独加工的部件组成,现在则是由3D打印成一块模制镍合金。
因此,数字制造技术的发展使个性化硬件的现场生产成为可能,为快速定制产品以满足特定需求创造了新机遇。在太空环境、医院、灾难现场和实验室中,这类技术的应用尤为重要。传统的集中式大规模生产模式难以根据个人需求和应用定制产品,因为它依赖于供应链的限制以及经济和政治的稳定。
本文从三个层面介绍了制造和装配自动化的方法
- 机器级:集成多个生产流程的制造机器。
- 组件级:可对部件进行重新配置的模块化组件。
- 材料级:可编程材料,材料本身可进行编程和组装。
这将使现场制造和装配自动化成为可能,从而能够生产出不同规模和不同应用领域的先进功能工艺品,如机器人、空间结构和分子机器。此外,还将介绍这些硬件平台的软件工具,使用户能够定义设计和装配协议。
如图 1.1 所示,本文介绍了如何利用这些分层装配技术实现制造和装配自动化。
图 1.1:机器级、组件级和材料级。在本文中,(1) 多工序制造机;(2) 模块化装配平台;(3) 材料级 (2) 模块化装配平台;(3) 可编程材料。 |
相关研究
与本文相关的主要研究领域简述如下。
1. 为机电设备制造电路轨迹:.
- 目前正在研究改进现有制造机械和自动安装电子元件的方法。
- 例如,在 3D 打印机中加入绕线装置,在提供长丝的同时提供导电线。
2. 扩大现有的生产设备:
- 目前已开发出使用激光切割机选择性烧蚀导电薄膜和放置电子元件的技术。
- 研究了利用激光烧结技术烧结银线以制造高导电性电路线的技术。
3. 模块化自组装重组:。
- 利用立方体模块开发出了可在二维和三维范围内重新配置的自重构机器人。
- 这包括使用电磁铁实现模块间驱动的方法。
4. 可折叠的模块化自组装:.
- 研究了使用形状记忆聚合物和形状记忆合金将低剖面薄片折叠成三维结构的技术。
- 这包括使用激光或局部加热来激活致动器的技术。
随机自组装:。
- 我们研究了使用廉价立方模块进行随机自组装的方法。
- 磁性像素用于创建模块,通过编程,这些模块只能以特定配置组合在一起。
6. 可编程磁性材料:.
- 研究人员利用哈达玛矩阵技术,对磁性像素阵列进行编程,使其自我组装成特定形状。
- 这表明该方案可适用于不同规模的材料。
如图 3.1 至图 3.7 所示,这些技术有许多潜在的应用,特别是基于激光的烧结和动态运动信号技术的最新研究。图 3.1 展示了一种硬件插件,可扩展激光切割机,用于创建电路轨迹和放置电子元件。
多工序制造机械
本节详细介绍了集成多种制造工艺的制造机械。它包括以下内容。
硬件附加组件
为了扩展现有的激光切割机,我们开发了一个硬件插件。该插件包括一个银分配器和一个用于放置元件的取放装置,可用于创建电路轨迹和放置电子元件(图 3.1)。
图 3.1:LaserFactory 是一种能够制造全功能设备的集成制造工艺。图 3.1:LaserFactory 是一种能够制造出功能齐全的设备的集成制造工艺。(a) 在现有激光切割机上添加的硬件包括一个银分配器和一个拾放机构。它不仅能切割形状,还能创建电路轨迹并组装电子元件。它能创建电路轨迹并组装电子元件。我们基于加速度计的运动插件无需更改固件即可与激光切割机连接。 |
硬件实施
如图 3.3 所示,硬件附加装置由一个机械装置组成,该装置连接到激光头上,产生银色轨迹并定位电子元件。此外,还使用了一个加速度计来检测运动信号并控制附加装置的移动。
图 3.3:硬件附加组件。物理设备。该插件包括一个用于创建电路轨迹的银分配器和一个用于组装电子元件的拾放装置。包括一个用于组装电子元件的取放装置。激光头用于创建器件几何形状和固化电路轨迹。该图像还显示了一个用于检测运动的加速度计,该加速度计可在插件开始/停止运行时发出信号。图片还显示了用于发出运动开始/停止信号的加速度计。 |
激光烧结
目前已开发出一种利用二氧化碳激光器的衰减功率烧结银线的激光烧结技术。这样就能生产出高导电性的电路轨迹(图 3.2)。
图 3.2:使用 LaserFactory 创建设备:(a) 切割设备的几何形状,(b) 点银形成电路轨迹,(c) 挑选和放置元件。(a)切割设备几何图形,(b)点银形成电路痕迹,(c)拾取和放置元件。四旋翼飞行器的旋翼。(这里,四旋翼飞行器直接从平台上升起。 |
激光烧结的生产设置
表 3.1 概述了激光烧结的制造设置,其中显示了工艺顺序、生产线操作、激光切割机设置、银分配器和拾放机构设置。
表 3.1:加工设置。从左到右依次为 (a) 加工顺序,(b) 生产线操作,(c) 激光切割机设置,(d) 配银机和拾放机构的附加设置。取放装置。斜杠表示数值可变。 |
创建非平面几何形状
激光烧结技术还可用于通过折叠创建 2.5D 几何形状,或通过切割和拾放材料基板本身创建离散 3D 几何形状(图 3.4)。
图 3.4:LaserFactory 可以通过折叠的方式制作出(a)2.5D 的形状,以及(b)通过对材料基板本身进行切割和取放的方式制作出离散的三维形状。(b)通过对材料基板本身进行切割和拾放,制作出离散的三维形状。 |
激光切割机的扩展动态信号。
利用运动信号技术,我们开发出了一种无需软件接口即可扩展现有制造平台的方法。这样就可以进行信号校准和实时分类(图 3.6 和 3.7)。
经过过滤的加速度计数据
如图 3.6 所示,在执行嵌入式模式期间,加速度会迅速变化,这一特性被用来生成启动/停止信号的控制信号。
图 3.6:嵌入式模式执行过程中经过过滤的加速度计数据。模式执行期间 模式执行时,(蓝色)加速度会产生一系列符号相反的尖峰。连续。(a、d)这一特征模板会导致(橙色)误差信号低于(绿色)阈值。当低于(绿色)阈值时,控制信号反转并启动/停止指令,开始/停止挤银。(b) 恒速期由接近零的加速度表示。(c) 不稳定的操作,如在连续线迹之间移动,会导致较大误差。(c) 在连续轨迹之间移动等不稳定操作会导致较大误差,可与生产文件中嵌入的实际运动信号指示区分开来。它们可以从以下方面区分开来。 |
信号分类的阈值校准
图 3.7 显示了信号分类的阈值校准方法,该方法使用数据集来区分正信号和噪声。
图 3.7:信号分类器的阈值特征。对信号进行采样,以构建真阳性数据集。对数据集进行采样,以构建一个真阳性数据集。将这些数据模型化为正态分布,并在其交点处设置阈值。区分信号和噪声。 |
激光工厂的设计与应用
激光工厂设计工具允许用户从零件库中选择零件、绘制几何图形和电路轨迹以及设计设备(图 3.8 和 3.9)。设计文件将被转换为机器指令并执行制造流程。
图 3.8:LaserFactory 生产流水线:(a)设计工具:用户放置元件,绘制几何图形和电路轨迹。(b) 可视化工具:用户可以预览三维设计,并对制造步骤进行可视化,以便对设计进行调试。(c) 后处理:导出设计文件后,设计文件将转换为扩展激光切割机的机器指令。(d) 制造:即切割几何图形、为电路迹线点银、拾取和放置元件、硬化银以使迹线导电以及烧结元件。制造完成后,设备即可完全投入使用。 |
图 3.9:用户使用设计工具栏设计四旋翼飞行器等设备。(a,e) 从部件库中放置部件,(b,f) 布线,(c,g) 绘制几何线,(d,h) 使用导出工具。渲染可视化工具的输出结果。 |
应用实例。
使用激光工厂制作的设备应用实例包括自部署四旋翼飞行器、个性化可穿戴设备和印刷电路板(图 3.11)。
图 3.11:使用 LaserFactory 制作的功能性设备:(a)可升降的四旋翼飞行器。(b) 带有能够进行手势识别的传感器的腕带; (c) 印刷电路板,尤其是 H 桥。 |
模块化自组装
本节将详细介绍通过重新配置进行模块化自组装的情况。
作动器
本研究提出了一种利用内置于每个立方体边缘的电磁铁实现模块间驱动的方法。这种方法利用相同磁极之间的排斥力和不同磁极之间的吸引力来转动模块(图 4.1 和 4.2)。
图 4.1:四个 Electrovoxels 是电磁致动模块,可在微重力状态下利用嵌入式电磁铁进行三维重建。它们可以在微重力条件下利用嵌入式电磁铁进行三维重建。 |
图 4.2:(上)转弯和(下)翻转的重新配置操作。红色和蓝色阴影表示电磁铁相对于全局坐标系的极性。相同极性相斥,相反极性相吸。 |
电磁铁参数
电磁铁参数包括电磁铁数量、绕组数量和电流值等细节,它们控制着驱动力(图 4.4)。
图 4.4:电磁铁力的计算。此处 D1、D2=10,线圈与线圈之间为一圈(力矢量为洋红色)。 |
动态模型
动态模型使用质量点模型模拟力的矢量和模块的运动。该模型可分析模块之间的动态相互作用(图 4.5)。
图 4.5:动力学模型。长度为 L 的无质量连杆(实线)连接着一个点质量 m。力 F 通过斥力驱动枢轴,而力 G 则吸引电磁铁,从而形成新的稳定连杆。 |
硬件
硬件设计涉及电子和机械设计。图 4.6 和图 4.7 详细介绍了电磁铁和电子元件的位置以及模块的机械结构。
图 4.6:电路板设计。(左)原理图,第 1 页,共 2 页 (右)布局,电路板 1/2. |
图 4.7:模块设计迭代。(左)第一个原型到(右)最终原型。 |
图 4.8:立方体模块的 CAD 模型。 |
电路板设计
电路板设计图显示了模块中电子元件的排列和连接(图 4.6)。
实验和结果
进行了二维和三维自重构实验,二维实验在空气台上进行,三维实验在抛物线飞行期间的微重力环境中进行(图 4.12)。
图 4.12:两个元件进行转弯动作 (a)。(a) 在用于模拟微重力环境的空气台上进行二维机动。(b) 微重力环境下的三维动作。 |
模拟结果
模拟结果显示了枢轴和移动操作的规划情况,评估了重新配置的成功率(图 4.3 和 4.9)。
图 4.3:用于规划重新配置和计算相关电磁指令的网络模拟。(A) 预设操作。(B) 视口。(C) 配置。 |
图 4.9:椅子、桌子和沙发之间的重新组合 |
实验结果。
二维和三维实验结果包括对重新配置成功率和模块间作用力的测量。其中,图 4.11 显示了力与电流和电磁铁之间分离距离的关系。
图 4.11:力 v 电流和电磁铁分离距离,显示 N=5 和平均 ±1 St.D. 的原始数据。为便于比较,图中显示了根据 (4.2) 预测的力和距离之间的关系。 |
讨论
根据实验结果,讨论了重新配置机器人的可扩展性和实用性。特别是,将对成本、复杂性和尺寸要求等问题进行研究,并对可扩展的自配置机器人的设计提出建议。
可折叠的模块化自组装
详细介绍了通过折叠进行模块化自组装的方法。
算法
我们开发了一种算法来生成可折叠的三维几何体。该算法展示了如何通过将三维网格制作成平面薄片,然后拉动薄片来创建三维结构(图 5.1)。
图 5.1:我们的数字制造流水线使用户能够快速制作三维物体原型:a) 基于网络的工具,用于上传和渲染三维网格。该工具会执行 (B) 解包算法,将网格展开成一个平面薄片,分成带有通孔的平面。(C) 然后用激光切割机对展开的形状进行加工,在孔中穿线,然后通过拉线将薄片折叠成所需的结构。 |
顶点集识别
如图 5.2 所示,识别顶点组并计算连接顶点组的螺纹方向。考虑到顶点集的深度,只进行必要的连接,从而最大限度地减少所需的螺纹数量。
图 5.2: (A) 确定需要用字符串连接的顶点集的算法图解。颜色代表需要连接的网的顶点,数字表示每个顶点的刚性深度。小箭头表示从每个顶点开始的搜索方向。此外,刚度深度为 1 的顶点不需要用线绳连接就能组装出最终立方体;在三维插图中,切割边用虚线表示。(b) 用一块十二面体网展示了相同的概念。深度 1 和深度 2 的顶点并不一定需要连接起来才能确定一个完全连接的几何结构。在所有这些顶点对之间添加一根绳子至少需要两倍的绳子,而且很可能会增加组装过程中的摩擦力,并使组装过程复杂化,因为其路径上需要几个急转弯。根据组装物体的功能和预期载荷,这可能是增加最终结构刚度的一个值得权衡的选择。 |
网络工具。
开发的网络工具允许用户上传三维网格,应用折叠算法并查看计算出的展开网(图 5.3)。
图 5.3:基于网络的可视化工具。(A) 该界面允许用户上传几何图形文件或选择几何图形文件,对几何图形应用折叠算法,并显示计算出的穿孔网。折叠过程的每个阶段都会显示穿孔网。(b) 折叠过程的各个步骤可视化。 |
人造结构和应用。
使用这种方法制造的结构有各种形状和规模,用途广泛,从教育工具到承重家具(图 5.4 和 5.5)。
图 5.4:使用我们的流水线制造的结构,规模从规则的多面体到有机体都有。从承重到美观不等,包括虚拟现实、教育和功能性承重环境。 |
图 5.5:多面体的制作。(A) 四个简单三维实体的无包装布局 (B,C,D,E) 折叠过程中制作的结构。 |
多面体的制作
图 5.5 展示了一个利用简单三维实体展开布局制造多面体的实例。通过拉线将薄片折叠成目标形状。
制造有机形状
图 5.6 展示了斯坦福 "兔子 "渲染、部署和制造流程,该流程也可制造复杂的有机形状。
图 5.6:有机形状的制作。(a)渲染,(b)拆包,(c)制作。斯坦福兔 |
拉网示例
如图 5.7 所示,可以通过拉动同时固定展开网的一侧来实现稳定的折叠操作。
图 5.7:使用拉网折叠三维多面体的示例:按照惯例,在折叠过程中,折叠网的一个表面(灰色)保持固定,在用户操作折叠时帮助稳定结构。 |
应用。
如图 5.8 所示,应用范围很广,从教育工具包到 VR 的低分辨率物理道具、书架和支撑负载的凳子。
图 5.8:(A-D)教授面积与体积关系的教育工具包;(E)按需制作虚拟现实的低分辨率实物道具;(F)书架和凳子等承重应用。 |
讨论
讨论了这种方法的优势和挑战。其中特别强调了这种方法的低成本和易于制造的特点,以及利用外部动力进行强力驱动的能力。另一方面,还讨论了材料选择和折叠操作控制方面的挑战。
可编程材料
本节将详细介绍可编程材料。
编码的生成
目前已开发出一种可编程材料编码生成方法。这种方法使用磁性像素来创建模块,通过编程,模块只能以特定的配置组合在一起(图 6.1)。
图 6.1:(左)利用廉价(0.23 美元)的立方体模块实现随机自组装。(上图,右)这是通过用基于哈达玛矩阵的编码对模块的面进行唯一配对的磁编程实现的,图中显示了其性能的界限。(下图,右)该模块成功的关键在于它能够被其方向对应模块强烈吸引,同时与所有其他平移、旋转和非方向模块无关。 |
图 6.2:随机自组织方法概述。(左)磁性像素:立方体模块采用磁性像素矩阵编程。这样,模块的各个面就能有选择地匹配和组装目标几何体。为清晰起见,图中显示的是 3x3 矩阵,但我们的模块使用的是 8x8 矩阵。 (左中)可扩展性:我们的二进制 8x8 矩阵可对 264 个模块面进行独特排列编码,而且模块价格低廉(0.23 美元)。(右中)选择性保证:我们使用哈达玛矩阵对平面上的磁像素进行编码,有两个标准。在 "局部 "情况下,配对平面只被一种配置吸引;在 "全局 "情况下,非配对平面不会被任何配置吸引。(右图)可重新配置性:使用放置在三轴数控系统上的磁铁将编码 "编程 "为磁性像素。该模块可重新编程,自行组装成新的目标几何形状。 |
矩阵搜索。
矩阵搜索算法用于生成编码模式。它根据哈达玛矩阵的顺序计算归一化二进制值的像素位置(图 6.3)。
图 6.3:(顶部)由阶数 N 为 2、4、8 和 16 的矩阵生成的归一化自然阶哈达玛矩阵。-1和-1的二进制值分别表示为暗像素和亮像素。(下图)其同伴。 |
磁性绘图仪
如图 6.6 所示,安装在三轴数控系统上的磁性绘图仪用于对模块的磁性像素进行编程。这样可以实现高精度编程。
图 6.6:磁力绘图仪: (a) 安装在三轴数控系统上的附加装置。(b) 从上方看附加装置的电子元件。(c) 绘图末端执行器特写,包括一个用于书写的带锥形尖端的电磁铁和一个用于读取磁性程序的霍尔效应传感器。 |
结果
对可编程材料的性能进行了评估,包括磁性程序的可靠性和最大磁场强度。
磁场强度的最大值
如图 6.7 所示,对电磁铁饱和时的磁场强度进行了评估。这证实了方案像素的强度。
图 6.7:电磁铁的 B-H 曲线。(a) 正极("北")和 (b) 负极("南")两端的电磁铁在 0.34 T 下处于饱和状态。 |
磁场的持久性
图 6.8 显示了薄片的磁滞曲线,并评估了完全饱和和未饱和时的磁场持续性。
图 6.8:薄片完全饱和时(主要回路,蓝色)和不完全饱和时(次要回路,红色)的滞后曲线。(a) 正负饱和度,(c) 正负残余通量,(e) 正负矫顽力。 |
磁性像素值读数的准确性
图 6.9 显示了使用霍尔效应传感器扫描的磁性像素值直方图,南北向像素清晰可辨。
图 6.9:霍尔效应传感器扫描的磁像素值直方图。朝北和朝南的像素清晰可辨。 |
预测的相互作用与测量的相互作用
图 6.10 评估了棋盘格图案和哈达玛矩阵之间的交叉相关性,并将预测的相互作用与实际测量的相互作用进行了比较。
图 6.10:当棋盘格和哈达玛矩阵的两个图案与它们的底片交叉相关时,预测和测量的磁相互作用。 |
可编程 DNA 组装
我们已经开发出一种方法,将可编程磁性材料的概念应用于 DNA 组装。这就实现了纳米级的自组装。
DNA 瓦设计
如图 6.18 所示,DNA 瓦片的设计和制造过程已经开发出来。这表明,方案化的 DNA 瓦片可以自行组装成所需的形状。
图 6.18:用于 DNA 组装的代码理论阵列翻译概述。(a) 使用 A、T、G 和 C 四值字母表将二维数组实例化为一维字符串。(c) 我们合成实际的 DNA,并将一维代码实例化为一系列空位和悬垂,旨在将特定悬垂序列与其互补空位结合。(d) 我们设计的方形瓦片可分层组装成更大的方形(左图)。原子力显微镜下的组装(右图)。 |
讨论和未来研究
本节对研究进行了总结,并讨论了未来的研究。
研究摘要
基于数字制造和硬件微型化的进步,本文开发了一种集成制造技术,可在单个平台上生产现场功能性人工制品。这为制造不同规模和不同用途的高功能人工制品(如机器人、空间结构和分子机器)创造了机会。
多工序制造机
在机器层面,已开发出激光工厂等多工序制造机,用于自动制造功能正常的四旋翼飞行器和健康可穿戴设备(图 3.1 和 3.2)。
模块化自组装
在组件层面,利用 Electrovoxel 等模块化自组装平台实现了二维和三维自重组(图 4.1 和 4.2)。
可编程材料。
在材料层面,磁性材料和脱氧核糖核酸已被用于开发可编程材料,这些材料能自我组装成特定形状(图 6.1 和 6.2)。
未来研究
今后的研究可侧重于以下领域
-
进一步整合生产设备:.
- 进一步整合多种制造工艺和开发技术,以生产具有更先进功能的工艺品。
- 通过整合新材料和新工艺,提高制造设备的性能和灵活性。
-
扩展自组装技术:.
- 改进模块设计和驱动技术,使更复杂的形状和结构能够自行重组。
- 开发纳米级和宏观应用的自组装技术。
-
可编程材料应用:.
- 开发新的编码方法和材料,为不同环境和应用创造可编程材料。
- 针对具体应用的应用研究,如医学和太空探索。
-
开发方便用户的软件工具:.
- 开发软件工具,使最终用户能够轻松定义设计和制造协议。
- 通过改进界面和增加自动化功能来改善用户体验。
结论
本文提出了一个整合多个制造流程的新平台,旨在实现车间制造和装配的自动化。具体而言,它展示了如何利用数字制造技术和机器人技术的进步,实现机器、部件和材料层面的制造和装配自动化。
主要贡献:
-
多工序制造机械:.
- 开发用于创建电路轨迹和放置电子元件的硬件插件。
- 使用 CO2 激光的烧结描银技术。
- 利用动态信号扩展现有制造平台。
-
模块化自组装:.
- 利用电磁铁实现模块间驱动的方法建议。
- 利用立方体模块开发三维自重构机器人。
-
可编程材料:.
- 开发使用磁性材料的模块,并通过编程使其仅在特定配置下耦合。
- 利用 DNA 演示纳米级自组装。
这些技术在快速现场响应和制造定制产品方面具有巨大潜力。特别是,它们有望应用于传统制造方法难以应对的情况,如太空环境和灾难现场。
未来研究
未来的研究将进一步开发该技术,目的是进一步整合制造机械,扩展自组装技术和可编程材料的新应用。此外,还将通过开发用户友好型软件工具,使最终用户能够轻松设计产品和定义制造协议。
希望本文提出的技术和方法能为未来的制造业迈出一步。
与本文相关的类别