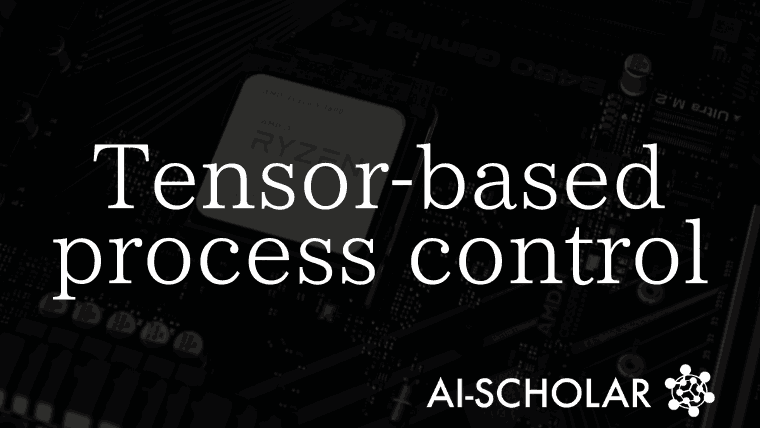
利用一个具有不稳定干扰的半导体制造过程实例,展示基于张量的过程控制性能
三个要点
✔️ 以半导体制造过程(尤其是光刻过程)中的位置叠加控制为主题,讨论了复杂数据的控制问题。
✔️ 通过建立高维过程模型并使用张量-矢量回归算法估算模型参数,缓解了维度诅咒。
✔️ 在张量参数估计的基础上,为张量数据设计了一个 EWMA 控制器,理论上保证了稳定性,同时监控控制残差,防止因不可控的高维干扰而导致的显著漂移。
Tensor-based process control and monitoring for semiconductor manufacturing with unstable disturbances
written by Yanrong Li, Juan Du, Fugee Tsung, Wei Jiang
[Submitted on 31 Jan 2024]
Comments: accepted by arXiv
Subjects: Machine Learning (stat.ML); Machine Learning (cs.LG); Image and Video Processing (eess.IV); Systems and Control (eess.SY)
code:![]()
本文所使用的图片要么来自论文、介绍性幻灯片,要么是参考这些图片制作的。
概述
为了应对从安装在制造系统中的传感器收集到的复杂数据,我们提出了一种新的过程控制和监控方法,以减少半导体制造过程中基于图像的高维叠加误差。该方法通过建立一个高维过程模型,并使用张量-矢量回归算法估算模型参数,来缓解维度诅咒。此外,在张量参数估计的基础上,为张量数据设计了一个 EWMA 控制器,理论上保证了稳定性。考虑到控制配方调整无法弥补所有高维干扰,因此对控制残差进行了监控,以防止因不可控的高维干扰而导致的显著漂移。通过大量仿真和实际案例研究,评估了 EWMA 控制器在参数估计算法和张量空间中的性能,并验证了与现有的基于图像的反馈控制器相比,所提方法的优越性。
介绍
以半导体制造工艺,特别是光刻工艺为重点,深入探讨了叠层错误检测和纠正的重要性。光刻工艺旨在最大限度地减少相邻材料层之间的错位,而这种错位会直接影响半导体器件的性能。减少叠层误差是确保高质量产品的关键。
为了准确识别叠加误差,晶圆上特定位置的误差测量要用图像表示。图 1 演示了这一过程,每个测量点的误差都用箭头表示,箭头的长度和方向表示误差的大小和方向。这种以图像为基础的表示方法能让人更直观地了解误差并进行精确修正。
图 1:晶圆上的叠加误差示意图 |
用于补偿叠加误差的控制配方包括晶片位置和方向、透镜高度等。调整这些参数可以补偿误差,提高制造过程的精度。然而,叠加误差的高维度和复杂性使得这些控制配方难以实现完全补偿。为了应对这一挑战,我们提出了基于张量的过程控制和监控方法。
建议方法的核心是有效处理从生产过程中收集的高维图像数据,并建立一个基于张量的过程控制和监控模型。该方法的框架如图 2 所示,包括高维参数估计、针对张量数据的 EWMA 控制器设计以及基于控制残差的监控策略。这提高了过程稳定性,并增强了制造过程对干扰的适应能力。
图 2. 基于张量的过程控制和监测 |
它详细介绍了所提出的基于张量的方法如何优于传统的控制方法,以及它是如何解决在处理高维数据时所面临的挑战的。考虑到流程数据的多维性和复杂性,基于张量的方法能够实现更有效的流程控制和监控。这有望提高半导体制造过程的效率、改善质量并降低成本。本文提供了详细的介绍,以便深入了解半导体制造行业当前面临的挑战以及拟议的基于张量的方法可能产生的影响。
相关研究
现有的过程控制和监测方法
运行到运行(R2R) 控制: 在包括半导体制造在内的许多复杂制造系统中,R2R 控制被广泛用于稳定一系列生产任务的质量。方法包括从单输入-单输出(SISO)系统到多输入-多输出(MIMO)系统,但这里的重点主要是单变量或多变量数据。
过程监控: 针对半导体制造过程开发了各种过程监控方法,包括基于 PCA(主成分分析)的方法和基于局部累积和统计的在线监控方法。虽然这些方法可以处理高维度和非高斯性质的数据,但在有效处理图像数据等更复杂的数据结构方面能力有限。
张量分析的应用
基于张量的回归: 张量分析正被应用于回归模型,以处理复杂结构和高维数据。这促使人们提出了新的张量回归方法,例如,脑成像数据分析中的张量变量回归模型,以及针对具有不同阶数的多个输入张量的多张量张量回归方法。
基于张量的监控: 基于张量的监控方法可用于异常检测和故障诊断。基于图像的过程监控方法,例如基于低等级张量分解的方法,可用于检测制造过程中的变化。
技术
本研究提出了一种方法,利用基于张量的方法,有效控制和监测半导体制造过程(尤其是光刻过程)中基于图像的高维叠加误差。该方法引入了处理高维工艺数据的新框架,并提供了具体的计算程序和实施细节。
问题的描述和提出
光刻工艺中的一大挑战是最大限度地减少以叠加误差形式表现出来的质量变化。这些误差是由晶片上多个层之间微妙的错位造成的。作者采用多维张量数据结构来表示这些叠加误差。以张量形式表示的模型定义如公式 (1),它允许以多维数组的形式捕捉每一层的错位。
B 是一个张量参数。
参数估计
张量-矢量回归算法用于估算流程模型的参数 B。这种估计方法是基本最小二乘法在张量空间的扩展,如式(2)所示,假设 B 存在于较低维度,以消除维度诅咒。此外,还引入了一种使用稀疏学习的估计方法,以提高参数估计的准确性和计算效率。算法 1 介绍了这种估计方法的详细步骤,并清楚地解释了每一步的计算过程。
图 4 显示了不同算法的比较。
图 4 不同算法张量参数估计的 PEE |
在线控制计划
所提出的控制方案将指数加权移动平均(EWMA)控制器应用于张量数据。该方法的稳定性在理论上是有保证的,其证明以方程 (10) 为基础。图 1 直观展示了该控制方案在实际过程数据中的应用实例,显示了控制前后叠加误差的改善情况。
残留监测
此外,还开发了一种使用张量控制图的监测方法。该方法通过分析控制残差,实时评估流程是否在计划控制范围内。具体的监控程序在算法 2 中进行了描述,包括设置各种控制限值的方法。表 1 概述了干扰和控制配方之间不同相关值的 MAE 值。在控制基于图像的质量变量时,确定了张量空间中 EWMA 控制器的稳定条件。
表 1:不同参数估计值的 MAE 摘要 |
案例研究
所提出的基于张量的过程控制和监控方法被应用于实际的半导体制造过程,并通过具体案例研究详细分析了其有效性。
不同过程控制器的比较
将所提出的 EWMA 控制器与传统的基于图像的反馈控制器进行了比较。具体而言,在相同的数据集上进行了仿真实验,以比较两种控制器的控制性能。表 2 和表 3 列出了每种控制器的统计性能指标(如平均误差、标准偏差),证实了所提出的 EWMA 控制器显示出更好的整体性能。
表 2. 基于 IMA 干扰的性能![]() |
表 3. 基于 ARIMA 干扰的性能
监测方法的性能分析
为了评估所提出的基于张量的监控方法的有效性,我们利用从实际生产线收集的数据,对四种情况下不同监控设置的影响进行了分析。分析特别评估了在早期阶段检测生产过程中异常情况的能力。
案例 A:平均移位。
案例B:分布式转移
案例 C:在综合管理评价过程中逐渐偏离。
案例 D:ARIMA 过程中的渐变漂移。
图 5 (a). 情况 A 的 𝑇2 和 𝑄 图 |
图 5 (b). 情况 B 的 𝑇2 和 𝑄 图 |
图 5 (c). 案例 C 的 EWMA 图 |
图 5 (d). 案例 D 的 EWMA 图。 |
通过本案例研究,展示了所提出的基于张量的过程控制和监控方法在实际生产环境中的有效应用。基于真实数据的详细分析进一步证明了该方法的有效性和实用性,并为未来的改进和潜在应用提供了宝贵的见解。
结论
随着传感器技术的广泛应用,质量测量不再局限于单变量或多变量,现在还包括基于图像的质量变量。它不再局限于单变量或多变量变量,而是包括基于图像的质量变量。本研究的重点是为具有基于图像的质量变量的平版印刷过程设计基于张量的过程控制和监控方案。本研究的重点是为具有基于图像的质量变量的平版印刷过程设计基于张量的过程控制和监控方案。输入控制变量数量有限 由于输入控制变量数量有限,干扰可分为两类。这两类干扰增加了高维张量参数估计的复杂性,使可识别参数估计和过程控制器设计变得非常复杂。 为了提高过程控制参数估计的准确性,现有的张量空间最小二乘估计算法通过稀疏学习进行了改进,以提高其极限,尤其是当离线数据集中的控制配方和第一类干扰高度相关时。然后将 EWMA 控制方案扩展到张量空间,以补偿第一类干扰,并针对第二类干扰引入不同的监控方法。重要的是,参数估计算法的特性和 EWMA 控制器的稳定性得到了保证。为了说明所提出的参数估计、过程控制和监控方法的效率,提出了大规模模拟和验证案例研究。通过与现有的基于图像的过程控制进行比较,发现 EWMA 控制在预测和补偿自相关不稳定干扰方面更具优势。最后,还利用T2、Q 和 EWMA 图表有效监测了制造环境中产生的第二种不同类型干扰的可变性,从而建立了一种全面的过程控制和监测方法。
与本文相关的类别