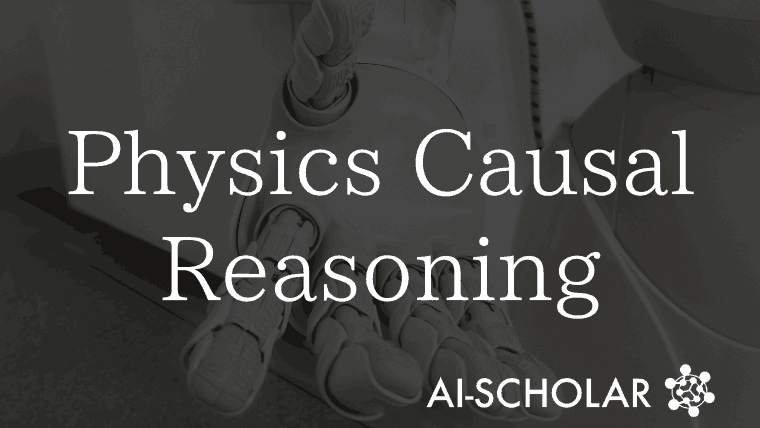
Giving The Robot An "eye Of Cause And Effect": Achieving A High Success Rate In Block Stacking Tasks
3 main points
✔️ A causal inference framework combining physics simulation and CBN achieved high performance in a robot block stacking task under uncertainty.
✔️ Simulation and real-world experiments demonstrated the high stability prediction and task success rate of the proposed method for block towers, confirming its real-world applicability.
✔️ The extension of the proposed method to an SCM-based system suggests the possibility of generating counterfactual explanations to improve the explanability and reliability of the robot's decision-making process.
Physics-Based Causal Reasoning for Safe & Robust Next-Best Action Selection in Robot Manipulation Tasks
written by Ricardo Cannizzaro, Michael Groom, Jonathan Routley, Robert Osazuwa Ness, Lars Kunze
(Submitted on 21 Mar 2024)
Comments: 8 pages, 9 figures, submitted to 2024 IEEE/RSJ International Conference on Intelligent Robots and Systems (IROS)
Subjects: Robotics (cs.RO); Artificial Intelligence (cs.AI); Machine Learning (cs.LG); Applications (stat.AP)
code:![]()
![]()
The images used in this article are from the paper, the introductory slides, or were created based on them.
Summary
In this paper, a physics-based next-best-move selection framework using probabilistic causal inference is proposed for a robot's block stacking task.The study shows that combining physics simulation and causal inference enables robots to perform block manipulation safely and reliably under uncertainty.
Introduction
Robotic object manipulation is a critical capability for many real-world applications, such as construction, assembly, and pick & place. However, robots face a variety of sensor and actuator uncertainties, making safe and reliable object manipulation a challenge.
To address this challenge, we propose a novel framework that combines physical simulation and probabilistic causal inference. Specifically, we model the decision-making process of a robot as a causal generative probabilistic model by integrating physical simulation of a rigid body system and causal Bayesian network (CBN) formulation for a block-stacking task.
Using this model, the robot can predict the stability of the block tower with high accuracy. Furthermore, it can probabilistically infer the position of the next block to be placed, taking into account the uncertainties of sensors and actuators. Simulation experiments have achieved a high prediction accuracy of 88.6% and a task success rate of 94.2%, and its effectiveness has been confirmed in actual machine demonstrations.
Related Research
Leveraging Causality for Robot Manipulation
Recent research trends indicate that causality plays an important role in reliable autonomous robotic systems. Specifically, the following issues are addressed.
∙ Machine learning approaches have problems with domain transfer, but causality could be used to solve this problem. (Pearl, 2019)
...can be an important tool for achieving desirable characteristics such as accountability, fairness, and accountability... (Ganguly et al., 2023; Lake et al., 2017)
Application of Causality to Robot Manipulation Tasks
On the other hand, the application of causality to robotic manipulation tasks has only recently been lima Specifically, the following issues are addressed.
Diehl & Ramirez-Amaro (2022, 2023) modeled a block stacking task as a CBN, learned/predicted task success probabilities, and performed action selection. However, there are issues such as the number of blocks and physical characteristics are not included in the model.
∙ CausalWorld (Ahmed et al., 2020) provides benchmarking in a physics-based simulation environment, but it is intended as a tool for policy learning and does not provide a framework for solving tasks online.
While research has begun to apply causality to robot operations as described above, the paper points out that challenges remain.
Proposed Method
The method proposed in this paper combines physical simulation and causal Bayesian networks (CBN) to formulate a causal generative probabilistic model of the robot's decision-making process.
The core of the proposed method is the causal diagram (Causal DAG) shown in the figure above. This diagram represents the decision-making process and system dynamics of the robot in a block stacking task consisting of two actions (k = 2). At each time step k, the robot chooses a stochastic action Ak based on the observed value Zk-1 of the previous tower state (with random noise WA,k), transitions the current hidden true tower state from Sk-1 to Sk, and obtains a noisy observed value Zk of the updated state (random with noise WZ,k). If the final tower state SN is stable, the task is considered a success, otherwise it is considered a failure. Observed variables are indicated by white circular nodes; unobserved variables are gray. Square nodes represent model parameters.
The proposed method uses this CBN model to predict the stability of block towers and select the next best action. The stability prediction estimates the probability that the tower is stable based on observations. Next best action selection calculates the stability probability of the resulting tower state for each candidate action and selects the action that yields the highest probability.
This method combines causal inference and physical simulation to enable robots to perform well under uncertainty in block stacking tasks. It is also expected to be extended to Structural Causal Model (SCM) in the future to enable counterfactual explanation generation and improve the explanatory nature and reliability of the robot's decision-making process.
Experiment
In this paper, two experiments were conducted to verify the effectiveness of the proposed method.
Predicting tower stability
∙ 1000 random 3-block tower configurations were generated in simulation and used as test data.
Thestandard deviation of the observed noise was set to σz = 0.469 cm.
・Varying the threshold value of the tower stability probability, classification indices such as F1 score, AUC score, accuracy, and repeatability were calculated.
・When the threshold value is 0.4, the best performance is achieved with an accuracy of 0.955 and a reproducibility of 0.868, demonstrating the high predictive ability of the model.
The figure above shows ROC and Precision-Recall curves based on the model's prediction of tower stability. These curves are very close to ideal performance, suggesting that the model's classification performance is very high.
Selection of next block placement location
Fifty tower configurations with two initial blocks were randomly generated in the simulation, and the third block placement position was selected by the proposed method.
The standard deviation of the positioning error was set to σa = 1.57 cm.
The standard deviation of the positioning error is set to σa = 1.57 cm. The stability probability threshold of the placement position is set to τstable,A = 0.80, and the clustering threshold is set to τcluster = 0.20. The clustering threshold is set to τcluster = 0.20.
We conducted 500 placement experiments, 10 for each configuration.
The proposed method achieved a task success rate of 94.2%, which is much higher than the heuristic central placement of 74.4%.
Heatmap visualization of predicted stability probabilities for candidate placement locations is shown for low (left) and high (right) uncertainty robot systems. It can be seen that with increasing uncertainty, the stability probability decreases as one approaches the edge of the Ground truth stability region.
We also confirmed the effectiveness of the proposed method in a real-world environment, as the task of stacking two blocks to three blocks was attempted five times on an actual Toyota HSR robot and succeeded four times (80% success rate).
These results experimentally confirm that the proposed method based on causal inference combined with physical simulation and CBN performs well in the robot's block stacking task under uncertainty.
Conclusion
Through experimental results, this paper demonstrates the effectiveness and practicality of the proposed method and shows that causal inference can help robots deal with uncertainty in manipulation tasks.
Extending the proposed method to SCM-based formulations and enabling counterfactual explanation generation suggests directions for future research to improve the explanatory nature and reliability of robot decision-making processes. It also suggests that combining causal reasoning with physical simulation is an important step forward in opening new possibilities for dealing with uncertainty in robot manipulation tasks.
Categories related to this article